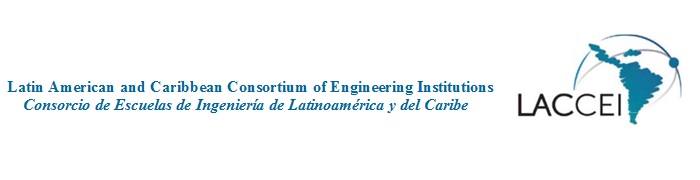 |
Design Proposal Of A Maintenance Management System For The Company Pesquera Pacasmayo E.I.R.L. |
Published in: | Prospective and trends in technology and skills for sustainable social development. Leveraging emerging technologies to construct the future: Proceedings of the 19th LACCEI International Multi-Conference for Engineering, Education and Technology |  |
Date of Conference: | July 19-23, 2021 |
Location of Conference: | Virtual |
"Authors: | Erick Quezada (Universidad Privada del Norte (UPN), PE) Lisbeth Pretel (Universidad Privada del Norte (UPN), PE) Carla Santamaría (Universidad Privada del Norte (UPN), PE) Nathaly Valencia (Universidad Privada del Norte (UPN), PE) Amanda Yépez (Universidad Privada del Norte (UPN), PE) Julio Cubas (Universidad Privada del Norte (UPN), PE)
|
Full Paper: | #57 |
|
Abstract:Abstract– The purpose of this study is to implement preventive maintenance in the company Pesquera Pacasmayo E.I.R.L. This study arises after identifying the constant problems in the production area among those that stand out in the
maintenance area. The study has a pre-experimental design in which a series of data collection techniques and instruments were used, specifically in the analysis of information on the company's production and maintenance processes. It begins by
making a diagnosis of these areas to identify the problems that directly affect productivity in order to determine the maintenance tools to apply; We proceed to find the Average Time between Failures considering the real-time work data and the number of failures, finding the value of 40 hours for the main machine, 70.94 hours for the Hydraulic Generator, and 54.36 hours for the Refrigeration Compressor, Average time between repairs considering the data of the stoppage time due to breakdown and the number of breakdowns, finding the value of 5 hours for the main machine, 3.5 hours for the Hydraulic Generator, and 4 hours for the Refrigeration Compressor, and the availability concluding that there is an availability of 89% for the main machine, 95% for Hydraulic Generators and 93% for
Refrigeration Compressors. Preventive maintenance was applied to minimize these problems, in addition to this, tools such as TPM were also applied. This is reflected in an increase in productivity, as well as an increase in total Team Effectiveness to 15%. |