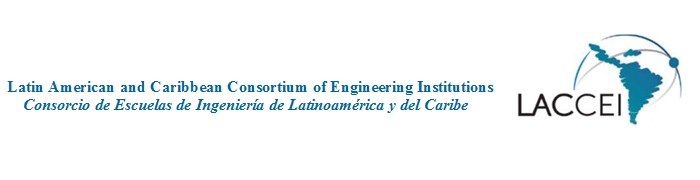 |
Lean Manufacturing Model of Waste Reduction Using Standardized Work to Reduce the Defect Rate in Textile MSEs |
Published in: | Engineering, Integration, and Alliances for a Sustainable Development. Hemispheric Cooperation for Competitiveness and Prosperity on a Knowledge-Based Economy: Proceedings of the 18th LACCEI International Multi-Conference for Engineering, Education and Technology |  |
Date of Conference: | July 27-31, 2020 |
Location of Conference: | Virtual |
Authors: | Nicole Barrientos-Ramos (Universidad Peruana de Ciencias Aplicadas, PE) Luz Tapia-Cayetano (Universidad Peruana de Ciencias Aplicadas, PE) Fernando Maradiegue-Tuesta (Universidad Peruana de Ciencias Aplicadas, PE) Carlos Arturo Raymundo-Ibañez (Universidad Peruana de Ciencias Aplicadas, PE)
|
Full Paper: | #356 |
|
Abstract:The textile industry currently represents 7.2% of the manufacturing companies’ GDP. However, it has experienced severe sales volatility owing to the high competitiveness, primarily mainly from Southeast Asian countries. Low productivity, process variability, operating cost overruns or long lead times are the main causes of the sector gap that must be attacked. Thus, this research is aims to contribute to the textile industry with methodologies and tools to gain a competitive advantage and reduce its operating cost overruns. We analyzed a real case study applied to a company called TEXTIL S.AC., following the implementation of combined work to integrate labor, work method, and machines to reduce the manufacturing cycle time by 300 seconds and, thus, waste such as defective products that generate expenses for the company. The results of the implementation and validation through process simulation showed an 8% reduction in the defect rate and a 32% improvement in the lead times. |