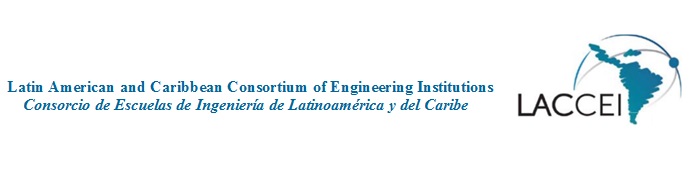 |
Diseño de Experimentos Optimizando un Proceso de Inyección de plásticos |
Published in: | Proceedings of the 13th Latin American and Caribbean Conference for Engineering and Technology: Engineering Education Facing the Grand Challenges, What Are We Doing? |  |
Date of Conference: | July 29 - 31, 2015 |
Location of Conference: | Santo Domingo, Dominican Republic |
Authors: | Juan Sillero Pérez
|
Refereed Paper: | #145 |
|
Resumen: |
La metodología del diseño de experimentos se usó para optimizar un proceso de inyección de plásticos en una fábrica de componentes de autopartes. Un estudio diagnóstico reveló la necesidad de reducir el tiempo de ciclo en una línea que produce ciertos componentes de plástico que se ensamblan y tienen el producto final denominado Intake Manifold, el cual es el filtro de entrada de aire para motores de combustión interna. Para optimizar el proceso de inyección se usó un diseño full factorial 24 con cuatro factores críticos en la operación y dos niveles cada uno: Hold time ( 4, 8 segundos), Pack pressure (660, 780 psi) , Shot size (7.7, 8.3 pulgadas) y Transfer position (1.33, 1.65 pulgadas); el resultado arrojó significancia estadística para los factores hold time, Pack pressure y Transfer position. Las condiciones óptimas encontradas fueron hold time 8 segundos, pack pressure 780 psi y Transfer position 1.65 pulgadas. Una vez llevadas al piso las nuevas condiciones de operación, se logró reducir los tiempos de ciclo de las inyectoras 15 y 17 pasando respectivamente de 80 a 65 segundos y de 78 a 65 segundos y con ello la eliminación del cuello de botella en el proceso.
Palabras clave- Autopartes, Intake Manifold, Optimización de procesos, Diseño de Experimentos, inyectoras de plásticos
|
Abstract: |
The methodology of Design of Experiments was used to optimize a plastic injection process in a factory to make auto parts components. Previous process efficiency diagnostic study revealed the need to reduce the cycle time on a line that produces certain plastic components that are assembled and have the final product called Intake Manifold, which is the air intake filter used in internal combustion engines. To optimize the injection process a full factorial design 24 was used with four critical factors in the operation and two levels each: Hold time (4. 8 seconds), Pack pressure (660, 780 psi), Shot size (7.7, 8.3 inches) and Transfer (1.33, 1.65 inches) position; the final results showed statistical significance for factors; hold time, Pack pressure and Transfer position. The found optimum conditions were hold time 8 seconds, pack pressure 780 psi and Transfer position 1.65 inches. Once carried out the new operating conditions, the cycle time of the process was improved in two injection machines. Machine 15 reduced its cycle times from 80 to 65 seconds, and machine 17 reduced its cycle time from 78 to 65 seconds. This new operational conditions eliminated the bottleneck in the process.
Key words-auto parts, Intake Manifold, processes optimization, design of experiments, plastic injection machines
|